Para la fabricación en serie se necesitan 4 turnos al día y un seguimiento especial por cada ladrillo fabricado
Contar con la planta más grande y moderna en América para la fabricación de ladrillos de arcilla industrializada requiere un gran reto. El inicio del proceso de fabricación es al pie de enormes montes de arcilla de por lo menos 15 metros de altura y donde sopla un viento frío. Aquí, la arcilla es llevada por enormes bandas para que a la intemperie se seque antes del siguiente proceso. Los montes son de arcilla mezclada que ya pasaron un proceso de molienda y homogenización. Y es precisamente en esta parte donde la arcilla todavía contiene muchos organismos, que se tienen que descomponer para que no provocar defectos en fabricación. El aire y el sol colaboran a lo largo de 45 a 60 días para que todo ese compuesto orgánico (ramas, hojitas, insectos o algún pequeño animal) se descomponga.
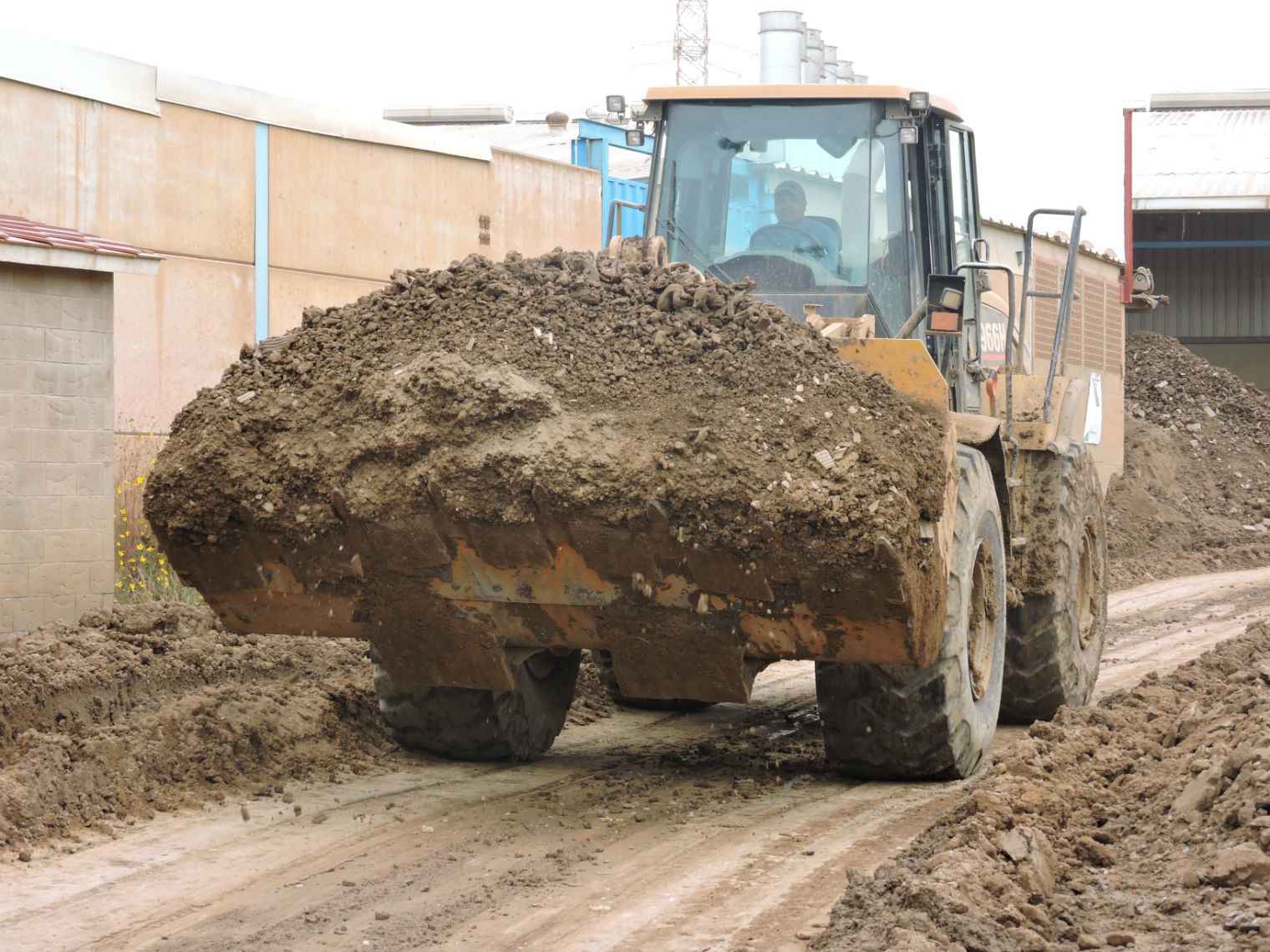
“El tabique que fabricamos esencialmente se hace con pura tierra sin agregados físicos, salvo cuando queremos darle alguna pigmentación especial. Esta arcilla contiene algunos compuestos químicos, pero esencialmente es tierra de diferentes lados. La mayor parte es tierra de la zona de tepetate que tiene una composición química especial que favorece mucho la fabricación de estos tabiques y el complemento son las arcillas plásticas que se extraen de la sierra norte de Puebla. La combinación de arcillas genéricas es la base para estos ladrillos especializados”, explica #Jonathan Nava, director de Mercadotecnia y servicio al Cliente de #Novaceramic.
Posteriormente, las arcillas ingresan en dos tolvas diferentes para mezclarse e ingresar a la sala de arcillas donde se van a estar moliendo, mezclando y amasando constantemente, una vez que salen del asoleadero; posteriormente regresan, se les da una última amasada y ya están listas para hacer los adoblocks.
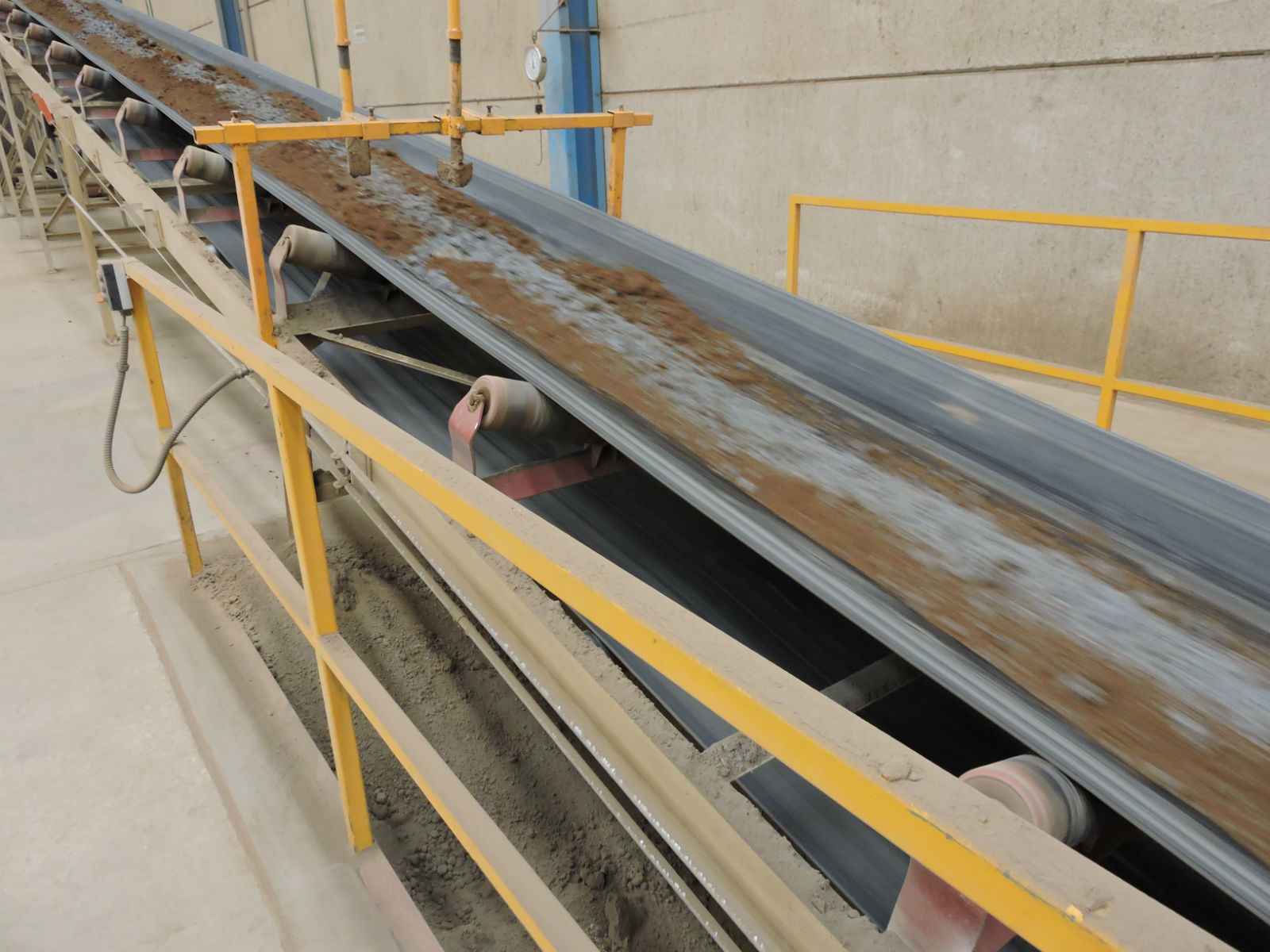
Es precisamente en estos rodillos en donde se van rompiendo las vetas de arcilla a través de un proceso de triturado, donde las bandas posteriormente las trasladan ya sin vetas grandes y empiezan a circular y entrar, en un proceso de mezclado a conciencia, donde tanto la arcilla genérica como la plástica terminan la primera parte del llamado proceso de tierra.
Una vez mezcladas las arcillas, se empuja el barro hacia un molde con hélices, donde se les dará forma. Cabe señalar que el proceso de homogenización necesita grandes instalaciones ya que en la mezcla el material está inerte e inorgánico. En esta parte se le adiciona agua en forma de vapor caliente para que todo el material tenga la misma temperatura y que a la hora de secarse quede homogénea.
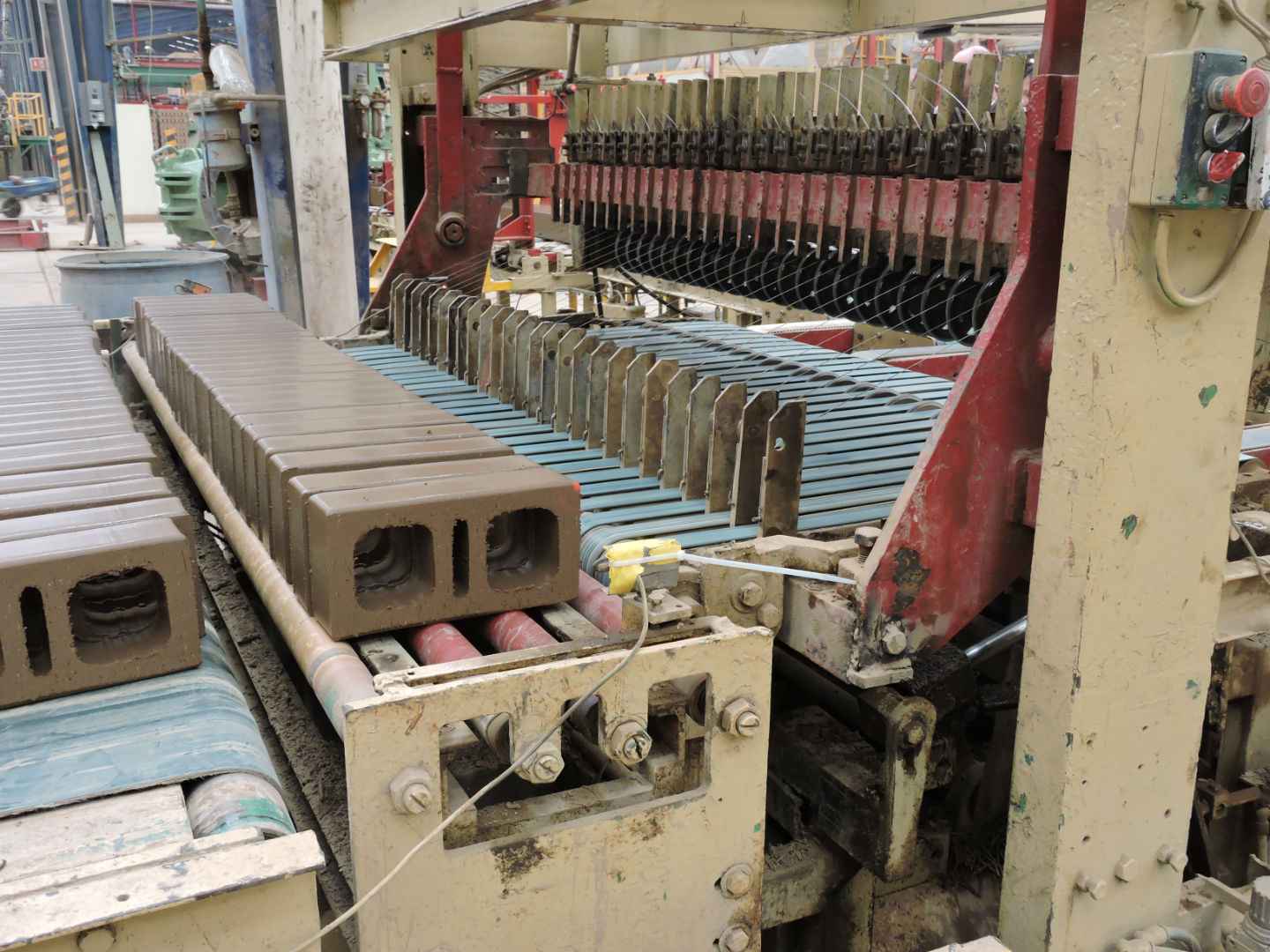
El riguroso proceso de calidad exige que cuando se pide algún acabado rústico se utilicen una serie de rodillos para textura, pero dentro de esa trazabilidad se marca el día de fabricación y así, si se presenta algún problema en obra se identifica el lote, ya que en todos los procesos de fabricación puede haber algún error, ya sea que falle un poco la máquina, baje la presión, se suba el nivel de humedad, o porque se rompa un alambre, pero tenemos un control de calidad en todas las áreas para detectar alguna falla, explica el director de Mercadotecnia.
Debido a la alta mecanización en estas fábricas, un error de 5 minutos implica 100 toneladas producidas, pero con este marcaje de calidad se detectan y corrigen fallas, ya que una fábrica de esta magnitud trabaja las 24 horas del día los 7 días de la semana, los 12 meses del año, donde se necesitan, para una labor de 24 horas, 4 turnos: 3 para cubrir las 24 horas y uno para dar vacaciones a los otros tres.
